Technical Cleaning of Parts and Components
The removal of residues accumulated on parts during the manufacturing processes (machining, stamping, welding, etc.), is a determining factor in guaranteeing the proper execution of the subsequent phases of the production cycle, as well as the storage of the finished part and its final dispatch to the customer, as the level of cleanliness of parts and components affects the quality of the final product.
Manufacturers are faced with technical issues that are often outside their area of expertise:
- The source of the dirt.
- The type of contaminant.
- How to characterise the dirt on a part or component.
- How the geometry, nature of the substrate and, above all, the nature of the contaminant affect the type of technique to use for the characterisation and analysis of the dirt.
- Which cleaning process is the most suitable.
- How the quality of a clean surface be controlled and guaranteed in the long term.
- When to act on the dirt.
In order to define the cleaning process, both its technological feasibility and its economic impact are decisive, making it necessary to find a balance between both factors.

Why incorporate a technical cleaning process?
Sectors such as the automotive, aeronautics, electronics and energy sectors, among others, require their suppliers to control and guarantee the level of surface cleanliness in order to:
What does CIDETEC offer?
We have the appropriate means to quantify the level of cleanliness of a surface, which, together with our experience and knowledge of industrial processes, allows us to quickly diagnose the source of the problem and provide the optimum solution:
1.
Study of the current process: detection, analysis and quantification of contaminants.
2.
Identification of the contaminant input and generation sources, as well as the stage in the manufacturing process at which they occur.
3.
Evaluation of critical stages in cleaning processes.
4.
Optimisation of cleaning processes.
5.
Starting up the processes: in-company implementation
6.
Design of installations and coordination with engineering companies and manufacturers.
Who is it for?
We address all those companies where the elimination of residual contaminants accumulated on parts during the manufacturing processes (machining, stamping, welding, etc.) plays a fundamental role in guaranteeing the proper execution of subsequent phases of the production cycle and their final dispatch to the customer..
Our capabilities and infrastructure
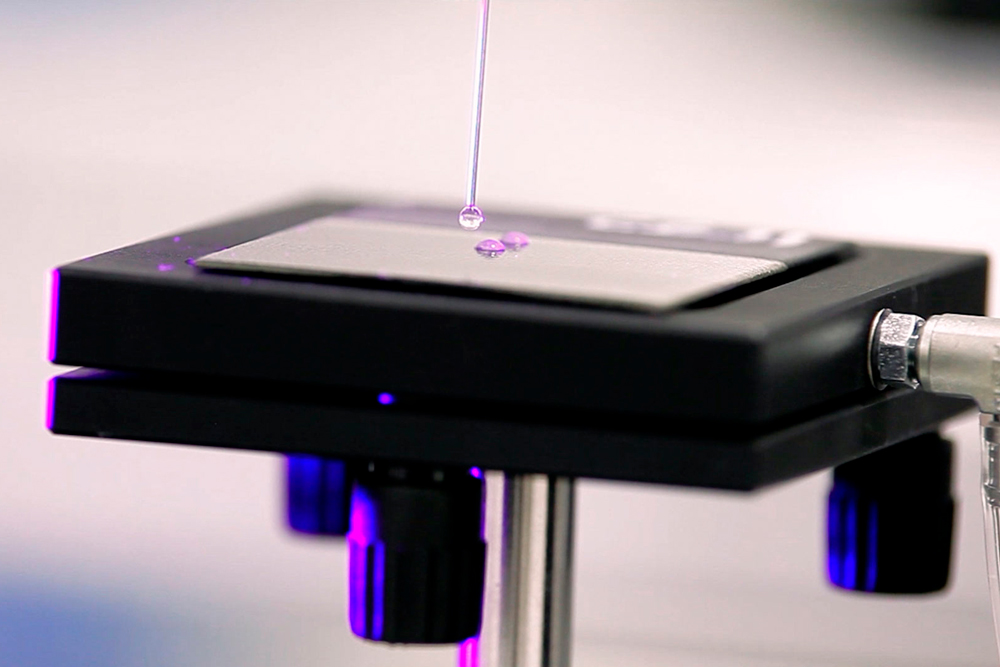
Contamination analysis, characterisation and control laboratories
CIDETEC has equipment to quantify the particle size and characterise the type of dirt, both organic and inorganic:
- Organic: from cutting fluids, adhesives, pastes, fluxes, etc.
- Inorganic: from residues of cleaning products, oxides, abrasives, metallic particles, etc.
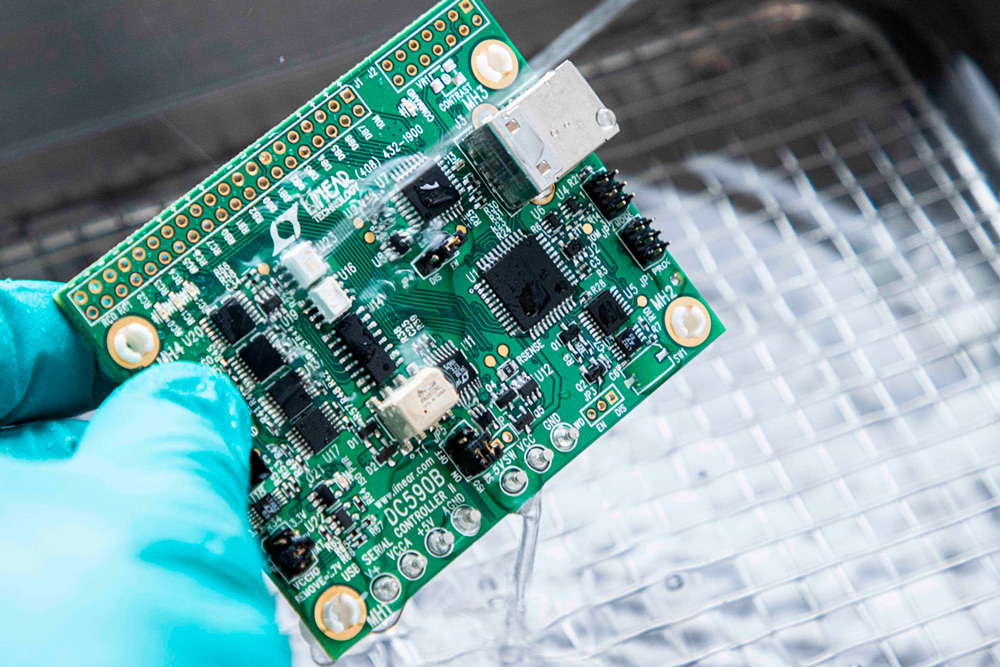
Cleaning processes
CIDETEC has unique equipment for the application of different cleaning processes, regardless of the base material, achieving the desired finish:
- Chemical processes: Aqueous degreasing, organic solvents and acid solutions.
- Electrochemical processes: Electrolytic degreasing.
- Plasma and laser cleaning.
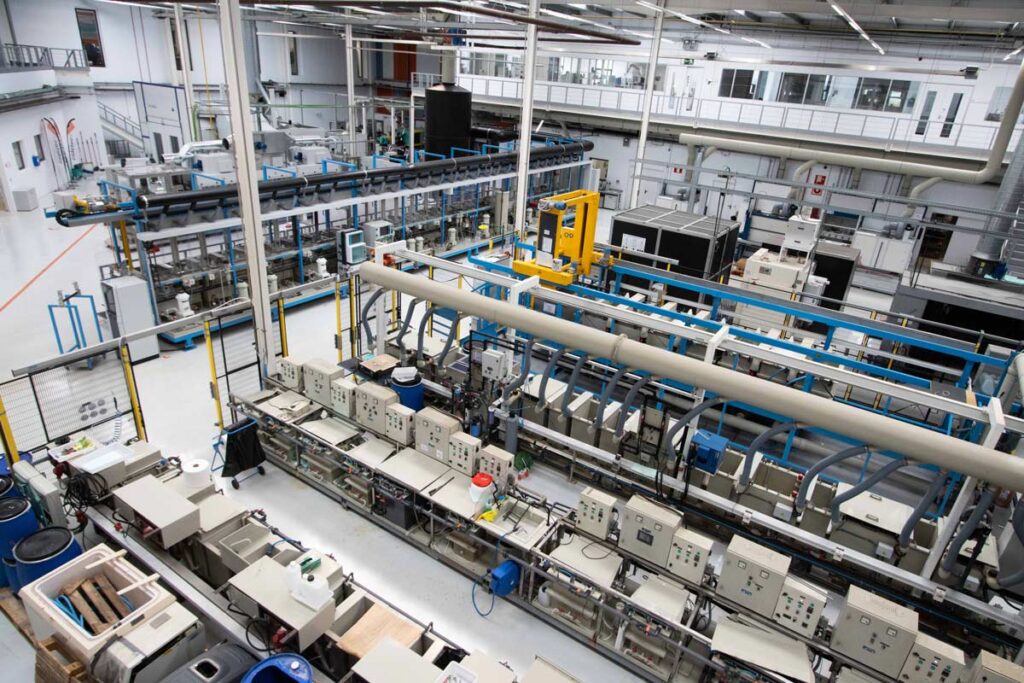
Pilot plants
CIDETEC has pilot plants that allow us to simulate and scale up industrial cleaning processes and, therefore, adapt the results to the most demanding finishing conditions.
Any questions?
For more information please contact us:
More information
"*" indicates required fields