Printed Electronics
In today’s technological-digital transition scenario, there is a growing demand for connected and interactive systems based on functionalized and/or sensorized surfaces. In this context, plastronics, also known as In-Mold Electronics (IME), is a new technology for manufacturing printed electronic devices embedded in plastic materials, providing high-value-added functions or features. Analyses and forecasts indicate that this technology will make electronics ubiquitous due to its wide range of applications in various sectors, such as:
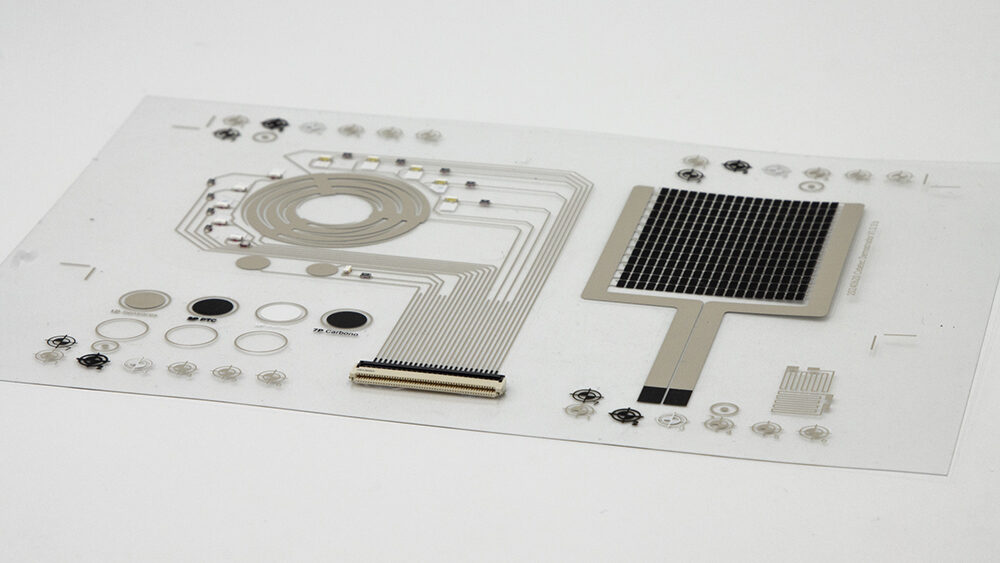
This manufacturing technology consists of four main processes:

Printing conductive inks (such as silver, copper, or carbon) using techniques like screen printing or inkjet on a flexible plastic film (typically PC, PET, or other polymers). Multiple layers are generally printed, which may include conductive, insulating, and decorative circuits.

Mounting SMD components such as LEDs, resistors, microcontrollers, etc., onto the printed film using automated placement methods (Pick & Place).

Once the entire electronic part is completed, the flat film undergoes a temperature and pressure or vacuum process to achieve the desired shape/geometry. This step is crucial to ensure that the electronics are compatible with curved or complex shapes that match the final design.

The thermoformed film is inserted into an injection molding mold. Plastic material (such as ABS, polycarbonate, or others) is injected onto the film, encapsulating the electronic circuits and creating a solid and durable final piece.
The result is a molded component with electronic circuits and components fully embedded in its surface or interior. The surface of the component can be interactive (e.g., touch panels) and may include additional features such as backlighting or LED signaling.
Why Printed Electronics? ¿Por qué printed electronics?
The advantages of printed electronics over conventional electronics include:
Weight Reduction
Flexible Design
Material Variety
Lower Costs
Sustainability
Our Developments Focus On:
- Functional Printing
- Decorative Printing
- Thermoforming
- Plastronics
- Composite Electronics
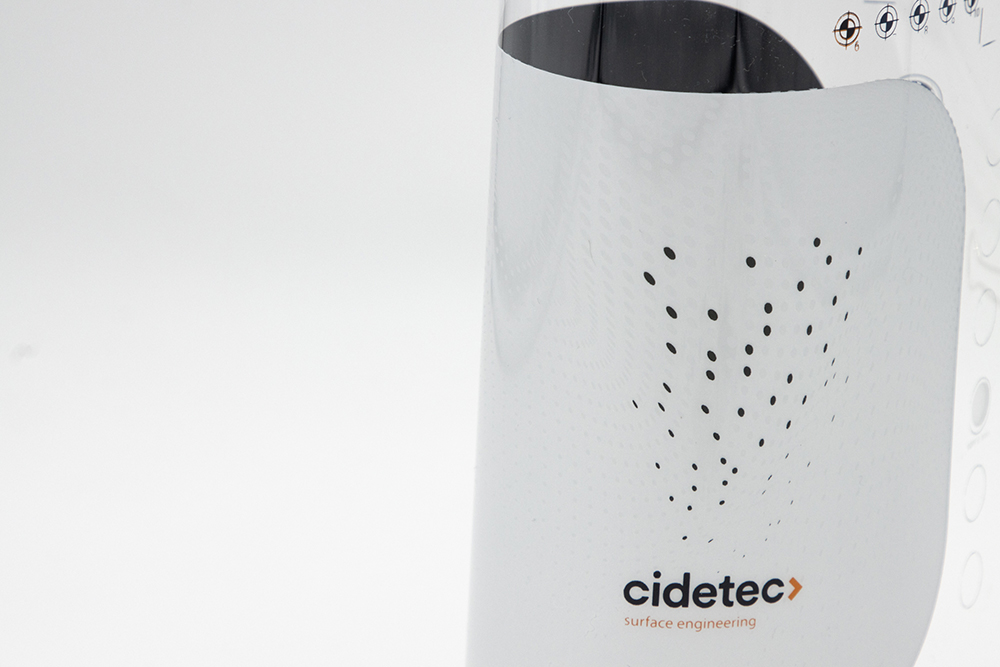
For Whom?
For the entire industry value chain across various sectors, with a special focus on automotive: chemical product suppliers, surface finishers, parts and component manufacturers, Tier 1 suppliers, and end-users/OEMs.

Automotive
This is the most demanding sector (80%) and the driving force behind the development of embedded electronics via IME for applications in displays, capacitive touch sensors, vehicle detection systems, instrument panels, ambient lighting, and any aesthetic-functional interior or even exterior vehicle parts. This technology is also relevant for electric vehicles due to its weight reduction compared to conventional electronics and the possibility of replacing wiring with printed circuits.

Home Appliances
White Goods: The second most demanding sector for this technology (10%), with its main application in high-aesthetic-quality touch controls on appliance front panels.

Health and Well-being
The third most demanding sector (4%), currently a key focus of research centers and several companies across Europe. Applications include patches for pain relief or sensors that can be attached to the patient’s body to monitor various health parameters. In terms of well-being, embedded electronics are found in wearable devices for sports and fitness.

Construction
Sensors and RFID (radio frequency identification) components are used in various IoT applications. One example is smart buildings, which continuously measure quality, temperature, or humidity levels and communicate data to the building automation system.

Energy and Photovoltaics
Flexible photovoltaics can be used as a sustainable energy source for both indoor and outdoor applications. These systems can be easily integrated into products of various shapes and sizes. Although Europe is not strong in the current crystalline photovoltaic market, it can position itself in the flexible photovoltaics sector. Embedded electronics are also useful for other energy applications, such as batteries and capacitors, which are currently in the development phase.

Smart Packaging
Smart packaging is a mature application that uses RFID and NFC systems for traceability/logistics or product status detection, in combination with various types of sensors.
Our capabilities and infrastructure
In addition to covering all stages of the IME process (printing, hybridization, thermoforming, and overmolding), CIDETEC spans the entire value chain, including modifying commercial inks to enhance performance and meet specific application requirements, designing electronic circuits (including tracks and component positions like LEDs, resistors, etc.), designing sensors, heaters, and other printed elements, as well as programming control electronics.
Furthermore, CIDETEC has the capability to integrate printed electronics into composite materials through C-RTM, prepreg, infusion, and thermoforming processes, based on its proprietary 3R (recyclable, repairable, reprocessable thermoset) technology.
- Semi-automatic Screen Printing Machines: SCREEN PRINTER THIEME 1000E and THIEME LAB 1000 (600)
- Ink-Jet Printer: FUJIFILM DIMATIX DMP-2831
- Vacuum Thermoforming Machine: FORMECH 508 FS
- High-Pressure Thermoforming Equipment: NIEBLING SAMK 720
- Pick & Place Machine: ESSEMTEC PUMA 1
- Injection Molding Machine: ARBURG ALLROUNDER 470S
- 3D Printing Machine: STRATASYS FORTUS 450
- Vacuum Dissolver Mixer: DISPERMAT® LH20
- RTM Machine: Isojet DPE COMPACT
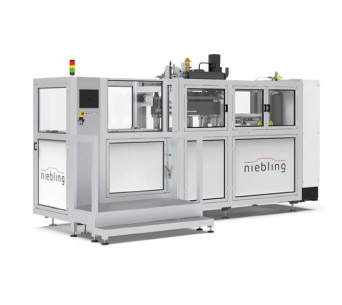
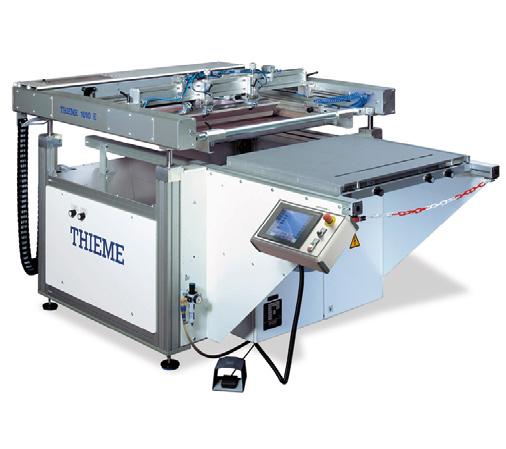
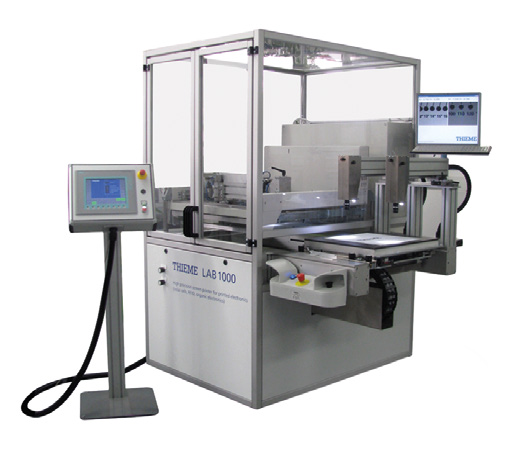
Any questions?
For more information please contact us:
More information
"*" indicates required fields