Metallisation of thermoplastics and fibre reinforced composites
The use of high-performance thermoplastics and fibre-reinforced composites has experienced rapid growth over recent years thanks to their high versatility, light weight, and eco-friendly properties. This allows their use in new applications and sectors, such as automotive and space, where outstanding surface properties are required.
The market demands robust components in which, apart from meeting eco-design criteria and technical requirements, perceived surface quality (i.e. the aesthetic, functional and, haptic properties and even the sound of the parts) is similar to metal.

Why Thermoplastics and Fibre-Reinforced Composites + Metallisation?
Thanks to their sustainability characteristics, polymeric materials are considered particularly suitable in tackling some of the greatest challenges of the 21st century.
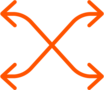


Meanwhile, metallisation is key to achieving the “metallic” properties demanded by the automotive, aeronautic, space and other sectors, enhancing polymeric surfaces in terms of:
Electrical and thermal
conductivity
EMI shielding
Aesthetics
Hardness
Wear and corrosion
resistance
Heat resistance
What do we offer?
CIDETEC Surface Engineering is committed to providing customised solutions and expertise on both bulk material (polymeric and composite) and surfaces, enabling companies to deal with unaddressed needs in the field of metallisation of thermoplastics and fibre-reinforced composites.
We are working on innovation areas with a particular focus on:
- Developing polymers and composites:
- Desarrollo de procesos de metalizado sostenibles personalizados:
Adaptados a la naturaleza de los polímeros y composites y sus requisitos funcionales y estéticos:- Most thermoplastic and thermoset materials are non-conductive, therefore making metallisation difficult, which is why specific protocols are needed to achieve proper anchoring.
- Conventional chemical metallisation processes are based on Cr(VI), which is considered toxic and carcinogenic. This is why new Cr(VI)-free eco-friendly metallisation processes are needed.
- Different functional and aesthetic properties require different metallic layers and application systems. To this end, CIDETEC masters the following technologies:
- Trivalent chromium plating
- Cr-free etching for metallisation
- Electroless metallisation (nickel, copper, etc.)
- Aero-plating
- Brush-plating
Who is it for?
For the whole coating industry value chain: chemical suppliers, surface finishing, parts and component manufacturers, end-users/OEMs.
End users:






Our capabilities and infrastructure
We work on different chemical and electrochemical processes for the metallisation of thermoplastics and fibre-reinforced composites.
We have an interdisciplinary team with strong skills and extensive experience in different industrial sectors, capable of carrying out cutting-edge research focused on different needs. Our fully equipped laboratories and pilot-plant facilities also allow our solutions to be applied and tested in pre-industrial conditions:

R&D laboratories for the design and synthesis of thermoplastics and fibre reinforced composites.

R&D laboratories for the design, synthesis, and chemical analysis of metallisation formulations.

Pilot lines for metallisation:
- Automated, digitally monitored galvanic pilot plants.
- Robotised brush plating plant.
- Robotised aerographic coating unit
- Inkjet and screen printing unit

R&D laboratories for testing and characterisation of coatings and materials: adhesion, morphology, composition, structure, aesthetics, wettability, roughness, hardness, scratch resistance, ageing and corrosion, etc.
Any questions?
For more information please contact us:
More information
"*" indicates required fields